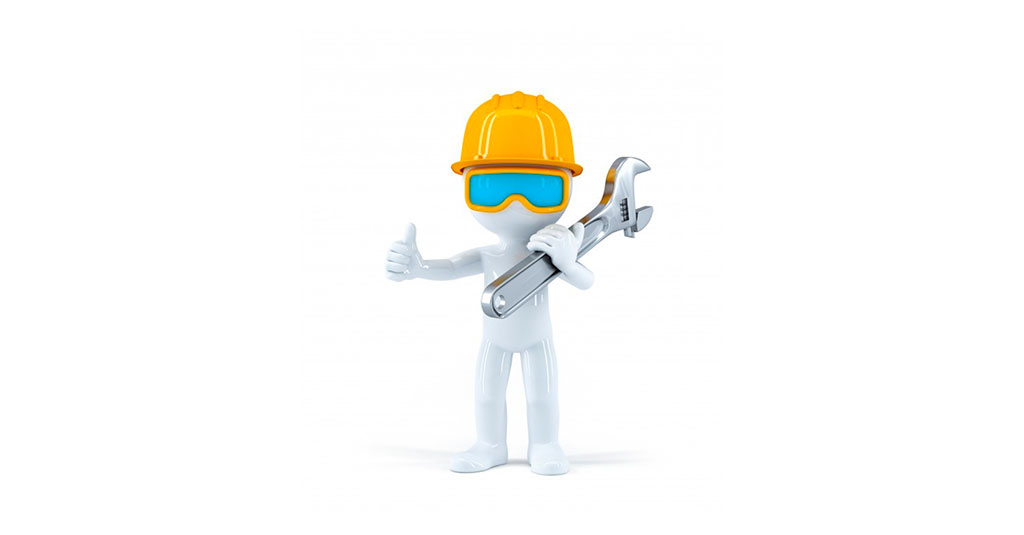
Wasting Money on deferred maintenance
“The cost of additional labor for unplanned or reactive maintenance and repair is higher than doing routine preventive maintenance because all of a sudden, you’re not in control of the resources,” Whittaker says. “Now you have higher overtime costs and possibly a need to bring in more expensive third-party contractors off hours to do work.”
“Assets that people often don’t associate with preventive maintenance are things like roofs, facades and parking lots that aren’t dynamic mechanical equipment. That kind of preventive maintenance can have a big impact because things like roofing systems and pavement are very expensive, and not fixing things and doing routine maintenance can really accelerate the deterioration and create a lot more expensive damage down the line”
“The equipment also usually doesn’t live to its expected life, so you’re having to do capital replacement sooner than if you had maintained it well to begin with. You’re also not getting productivity. If a piece of critical equipment fails, are you just going to send everybody home for a few days while you find the parts to fix it? You’re not helping your company by having all these unexpected severe events.”